Read this short guide to learn when you should replace, retire, relocate, or retain your forklifts.
Reliability is often the most sought-after trait by fleet managers. Warehouses need a forklift fleet that is reliable, and the best fleet managers know that this does not happen by accident. A reliable fleet is built proactively, with increased attention to planned maintenance and a keen observance on the fleet’s data.
Even with the fleet dialed in and charted, it may be still difficult to know when the optimal time to replace, retire, relocate, or retain certain forklifts. Replacing a forklift too soon means you risk not getting the most of your investment. Replace a forklift too late and you may risk an expensive and time-consuming breakdown.
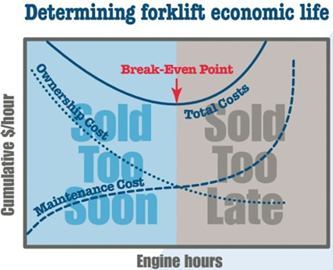
Breakdowns
A forklift past its prime may cost you more than you realize. After many years of service, you may experience worn forks, damaged structures, or hydraulic leaks. And when it comes to forklift maintenance, as the old saying goes, sometimes when it rains, it pours. Once breakdowns begin happening, it may be difficult to troubleshoot the issue and manage the costs effectively to keep everything running smoothly.
If you experience issues with a “trouble asset” and struggle to avoid downtime, it may be time to replace that forklift.
Downtime: The Actual Cost of a Breakdown
Breakdowns cost far more than the immediate price of the repair, it can also cost valuable time and significantly decrease the warehouse’s productivity. Minimizing forklift downtime is crucial, as unwanted breakdowns can heavily impact productivity. If a forklift breaks down, you may need to run a shift with one less operator, limiting productivity and increasing stress on the remaining operators.
To avoid any unnecessary downtime, it is important for you to focus on planned maintenance. Keep that in mind and always keep up with any recommended service for your forklift.
Plan Your Exit Strategy
When it is time to replace a forklift in your fleet you must plan carefully. First, it is important to proactively plan an exit strategy for your new forklift. Consider the environment in which the forklift will operate. Will it be used in a general environment or a high-use environment? The general guideline to follow for most forklifts is to replace a forklift around 10,000 hours, a high-usage environment is around 8,000 hours. But how will you track that usage?
Tracking your Fleet’s Utilization & Repairs
It is important to keep records of maintenance history and track the utilization rate for each forklift. When your forklift utilization rate goes over ninety percent, it is typically an overworked forklift. Often action is required, or you may need to add an additional forklift to your fleet.
Keeping detailed service records and tracking utilization rates can be difficult to perform when done manually, so we recommend utilizing a fleet management system. The current recommended fleet management system is Fleet Track.
Fleet Track offers a practical and efficient fleet management tool that provides a user-friendly interface and enhanced functionality to generate a comprehensive overview of your entire forklift fleet. The program also allows you to track utilization rates for each forklift, and the data collected can help guide you to make important decisions on whether to retire, replace, retain or relocate a forklift based on its cost per hour and utilization rate.
Using data to make the most educated decisions about your forklift will help you save time and money while increasing your efficiency and productivity. Using a fleet management system to collect and analyze that data can help you make the most out of your forklift fleet in the easiest way possible.
Have any questions? Contact Fallsway today!